How To Calculate Cost Of Goods Sold
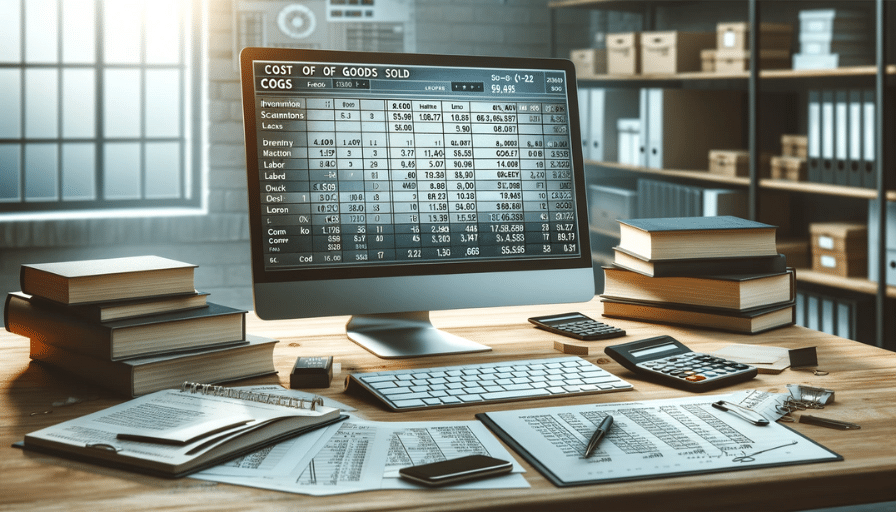
In this article, we will guide you through the process of calculating the cost of goods sold. Understanding this concept is crucial for any business owner, as it allows you to determine the profitability of your products and make informed decisions about pricing and inventory management. We will break down the calculation step by step, providing you with clear and practical examples along the way. By the end of this article, you will be equipped with the knowledge to accurately calculate the cost of goods sold for your business. So, let’s get started!
Understanding Cost of Goods Sold
Definition of Cost of Goods Sold (COGS)
Cost of Goods Sold (COGS) refers to the direct costs incurred by a company in producing and delivering the goods or services sold to customers. It includes the cost of materials, labor, and overhead expenses directly associated with the production process. COGS is a critical financial metric that helps businesses understand the amount of money they spent on producing the goods or services that generated revenue during a specific period.
Importance of COGS in Financial Analysis
COGS is crucial in financial analysis as it helps assess a company’s profitability and efficiency. By deducting COGS from the revenue generated, businesses can determine their gross profit. Monitoring COGS over time allows companies to identify trends, make informed pricing decisions, and evaluate the effectiveness of cost control measures. Additionally, COGS is a key component in calculating the gross margin ratio, which measures the profitability of each sale and provides insights into a company’s pricing strategy and cost structure.
Role of COGS in Inventory Management
COGS plays a vital role in inventory management as it provides valuable information to optimize the inventory levels. By analyzing the COGS data, businesses can determine the optimal quantity of finished goods to produce or purchase, ensuring efficient utilization of resources and avoiding excess inventory. Furthermore, COGS helps to identify slow-moving or obsolete inventory, enabling businesses to make informed decisions about inventory turnover, pricing adjustments, and product discontinuation.
Identifying Components of Cost of Goods Sold
Direct Material Costs
Direct material costs are the expenses associated with the raw materials used in the production process. These costs include the purchase price of materials, transportation costs, import duties, and any other expenses incurred in acquiring the necessary materials. To accurately calculate COGS, businesses need to track and record the direct material costs for each unit of product manufactured or sold.
Direct Labor Costs
Direct labor costs refer to the wages, benefits, and other expenses associated with the employees directly involved in the production process. This includes the workers who physically assemble, manufacture, or customize the products. Tracking and allocating direct labor costs to each unit of production are essential for calculating COGS accurately.
Factory Overheads and Indirect Expenses
Factory overheads and indirect expenses encompass all other costs incurred in the production process that cannot be directly attributed to a specific product or unit of production. These expenses include rent, utilities, machinery maintenance, depreciation, and indirect labor costs. To calculate COGS, businesses need to allocate a portion of these overhead and indirect expenses based on a systematic and rational method, such as allocating them proportionally to the direct labor or direct material costs.
Periodic vs Perpetual Inventory System
Key Differences
The periodic inventory system involves manually adjusting and updating the inventory records periodically, typically at the end of each accounting period. In contrast, the perpetual inventory system relies on real-time tracking of inventory levels through the use of technology, such as barcode scanners and inventory management software. The perpetual system provides up-to-date and accurate inventory data, while the periodic system requires physical inventory counts and adjustments, which are prone to errors and can be time-consuming.
Impact on Calculation of COGS
The choice between the periodic and perpetual inventory systems significantly impacts the calculation of COGS. In the periodic system, COGS is determined by subtracting the ending inventory from the beginning inventory, adding the cost of purchases during the accounting period, and subtracting any purchase returns or allowances. In contrast, the perpetual system allows for real-time tracking of inventory changes, ensuring accurate cost allocation and providing immediate insights into COGS.
Procedure for Calculating Cost of Goods Sold
Collecting necessary data
To calculate COGS accurately, businesses need to collect and organize various data. This includes documentation of all direct material costs, direct labor costs, and factory overhead expenses associated with the production process. It also involves maintaining accurate records of inventory levels, both at the beginning and end of the accounting period, as well as any purchases, returns, or adjustments made during that period.
Identifying relevant expenses
Once the necessary data is collected, it is important to identify and categorize the relevant expenses that directly contribute to the production of goods or services. This involves carefully reviewing the documentation and determining which costs should be included in the calculation of COGS. It is crucial to follow consistent and standardized accounting practices to ensure accurate and comparable calculations.
Generating the COGS formula
Based on the identified components and their respective costs, a COGS formula can be generated. The formula typically includes the sum of direct material costs, direct labor costs, and allocated factory overhead expenses. This formula provides a clear and systematic approach for consistently calculating COGS, allowing businesses to measure their production costs accurately.
Calculation Method for Retail Businesses
Retail Inventory Method
The retail inventory method is commonly used by retail businesses to calculate COGS, especially when they sell a wide variety of products. This method estimates the cost of ending inventory based on the retail price and applies a cost-to-retail ratio to determine the cost of goods sold. It is particularly useful when the exact cost of each item sold is not readily available, as is often the case in retail operations.
Gross Profit Method
The gross profit method is another approach used by retail businesses to estimate COGS. It calculates the cost of goods sold by subtracting the estimated gross profit from net sales. This method is typically employed when there are significant fluctuations in inventory levels or when physical inventory counts are not feasible or practical. While it provides an estimation rather than an exact calculation, it offers a reasonable approximation of COGS.
Last-In, First-Out (LIFO) Method
The Last-In, First-Out (LIFO) method is a widely used inventory valuation method that affects the calculation of COGS. Under LIFO, the most recent inventory purchases are assumed to be the first ones sold, resulting in a higher cost of goods sold. This can be advantageous in times of rising prices, as it reflects the higher cost of replacing inventory. However, LIFO may not accurately represent the actual flow of goods in some industries and can be more complex to implement than other methods.
Calculation Method for Manufacturing Businesses
Work In Process Inventory
For manufacturing businesses, calculating COGS involves considering the costs associated with work in process inventory. This includes the direct material costs, direct labor costs, and a portion of the overhead expenses related to the partially completed products. By properly allocating these costs, manufacturing businesses can determine the value of the work in process inventory and incorporate it into the COGS calculation.
Finished Goods Inventory
In addition to work in process inventory, manufacturing businesses must also consider the cost of finished goods inventory when calculating COGS. This includes the direct material costs, direct labor costs, and allocated overhead expenses associated with the completed products. By accounting for the value of the finished goods inventory at the beginning and end of the accounting period, manufacturing businesses can accurately calculate their COGS.
First-In, First-Out (FIFO) Method
The First-In, First-Out (FIFO) method is commonly used in manufacturing businesses to value their inventory and calculate COGS. Under FIFO, the oldest inventory items are assumed to be the first ones sold, resulting in a lower cost of goods sold compared to the LIFO method. FIFO generally aligns more closely with the actual flow of goods and can provide a more accurate representation of the cost of producing goods over time.
Common Mistakes in Calculating Cost of Goods Sold
Ignoring indirect costs
One common mistake in calculating COGS is failing to consider indirect costs associated with the production process. This can result in an incomplete and inaccurate estimation of COGS. It is important to ensure that all relevant expenses, including factory overhead and indirect expenses, are properly identified and allocated to the calculation of COGS to obtain an accurate representation of production costs.
Improper categorization of expenses
Another mistake is the improper categorization of expenses, leading to inaccurate COGS calculations. It is essential to classify expenses correctly, distinguishing between those that should be included in COGS, such as direct material costs and direct labor costs, and those that should be excluded, such as selling and administrative expenses. Proper categorization allows for a more precise calculation of COGS and better financial analysis.
Misinterpretation of inventory data
Misinterpretation of inventory data can also lead to errors in calculating COGS. It is crucial to maintain accurate and up-to-date inventory records, ensuring that the beginning and ending inventory values are correctly recorded. Failing to account for inventory adjustments, returns, or damaged goods can result in an unreliable calculation of COGS and misrepresentation of a company’s financial performance.
Tools and Software for Calculating COGS
Inventory Management Software
Inventory management software can greatly facilitate the calculation of COGS by providing real-time visibility into inventory levels, tracking purchases and sales, and automating data collection. These software solutions often include features such as barcode scanning, automatic cost allocation, and detailed reporting, allowing businesses to streamline their inventory management processes and enhance the accuracy of their COGS calculations.
Accounting Software
Accounting software plays a significant role in calculating COGS as it provides a comprehensive platform to track and record all the necessary financial data. These software solutions usually include features for inventory management, expense categorization, and generating financial statements. By leveraging accounting software, businesses can ensure accurate and efficient COGS calculations, reducing the likelihood of errors and providing a solid foundation for financial analysis.
COGS Calculator
For smaller businesses or those without dedicated inventory or accounting software, COGS calculators can be a valuable tool. These calculators typically include pre-defined formulas and templates that assist in collecting and organizing the necessary data for calculating COGS. They can help businesses streamline the process and ensure accurate calculations without the need for complex software or extensive accounting knowledge.
Impact of COGS on Profit and Loss Statement
Influence on Gross Profit
COGS significantly impacts the gross profit of a company, which is calculated by subtracting COGS from the net sales revenue. A higher COGS results in a lower gross profit margin, indicating that a larger portion of the revenue is being consumed by production costs. Monitoring the trend of the gross profit margin provides insights into a company’s ability to control production costs and maintain profitability.
Effects on Net Income
COGS also affects the net income of a company. After deducting operating expenses from the gross profit, the resulting figure is the net income. By controlling and managing COGS effectively, businesses can improve their net income by minimizing production costs and maximizing profitability. Understanding the relationship between COGS and net income is crucial for businesses to make informed financial decisions and optimize their overall performance.
Role in Earnings Before Interest and Taxes (EBIT)
COGS is an integral part of the Earnings Before Interest and Taxes (EBIT) calculation. EBIT represents a company’s operating profit and is calculated by subtracting operating expenses, including COGS, from the gross profit. EBIT is a key metric used to assess a company’s operational performance and profitability before considering the impact of interest and taxes. By accurately calculating COGS, businesses can obtain reliable EBIT figures, providing valuable insights into their financial health.
Strategies to Minimize Cost of Goods Sold
Negotiating with Suppliers
One effective strategy to minimize COGS is to negotiate with suppliers to obtain favorable pricing and terms. Building strong relationships with suppliers and exploring options for bulk purchasing discounts or long-term contracts can help reduce the direct material costs and, consequently, the overall COGS. Effective negotiation skills and proactive supplier management can provide businesses with a competitive advantage and cost savings.
Efficient Inventory Management
Efficient inventory management is essential to minimize COGS. By closely monitoring inventory levels, implementing just-in-time inventory practices, and regularly reviewing and adjusting ordering quantities, businesses can minimize carrying costs and avoid unnecessary overstocking or stockouts. Effective demand forecasting, continuous process improvement, and accurate record-keeping contribute to optimizing inventory management and reducing COGS.
Outsourcing and Automation
Outsourcing certain aspects of the production process or automating repetitive tasks can be an effective way to minimize COGS. By leveraging external suppliers or implementing automated systems and machinery, businesses can reduce direct labor costs, improve efficiency, and ensure consistent quality. Careful evaluation of the cost-benefit analysis and strategic sourcing decisions can help businesses achieve cost savings and enhance their competitive position.
In conclusion, understanding and accurately calculating cost of goods sold (COGS) is essential for businesses to assess profitability, optimize inventory management, and make informed financial decisions. By identifying the components of COGS, choosing the appropriate calculation method based on their industry and inventory system, avoiding common mistakes, leveraging tools and software, and implementing strategies to minimize COGS, businesses can enhance their profitability, efficiency, and overall financial performance.